A dedicated Application Development Center helps OEMs along the entire machine development life cycle
This article was first published in the iVT Magazine, June 2020
By Michael Thomas Mastera, product marketing manager at TTControl
Today’s mobile machinery manufacturers face constant technological challenges. They have to implement increasingly complex electronic architectures. In parallel, market conditions are rapidly changing, requiring OEMs of mobile machinery to keep up with the latest innovations and international standards. While in the past mobile machinery such as excavators, tractors including agricultural implements or waste collection trucks were solely be seen as a simple tool to get work done, machines nowadays have become smart and efficient and will be a collaborative partner for machine operators in the near future.
OEMs are even more in need of support from their suppliers for the crucial software application development to keep up with market needs or even set new standards. Therefore, suppliers of electronic solutions and systems must work closely with their customers in a collaborative, cross-functional partnership.
Thus, creating additional value during the software development for mobile machinery, to maximize efficiency and performance - not only for the machinery but also for the entire development process according to the V-Model.
Hurdles on the way to meet market demands and innovate
TTControl, a joint-venture company of TTTech Group and HYDAC International, offers control systems, operator interfaces and IoT solutions for mobile machinery and off-highway vehicles. As a leader in functional safety, its hardware and software platforms enable equipment manufacturers to develop highly reliable electronic control systems quickly and economically. TTControl detects four main challenges faced by mobile machinery OEMs that want to meet market demands and innovate:
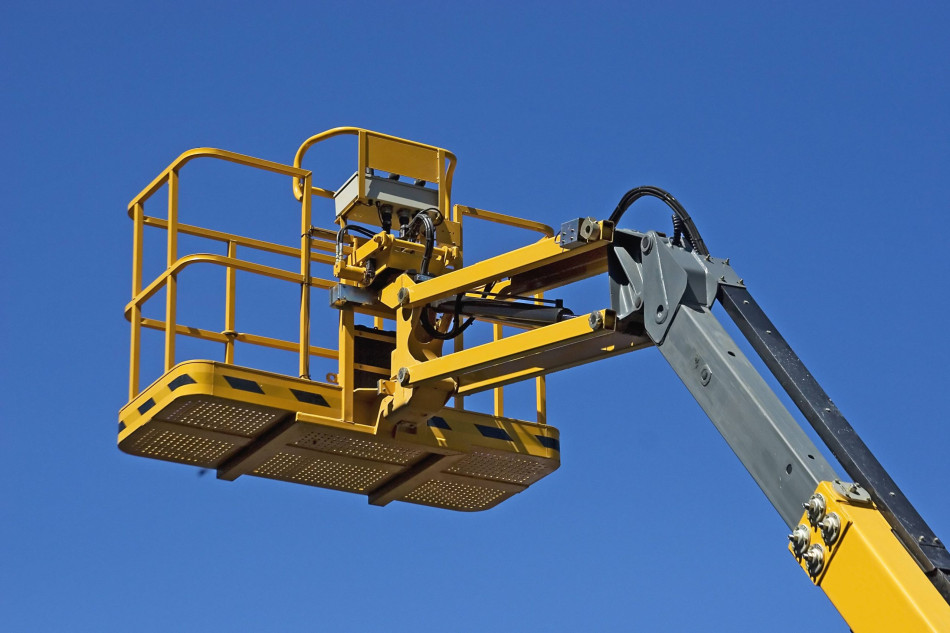
1. Increase in software complexity
2. Market pressure for time-to-market innovations
3. Restricted qualified personnel resources, tools and costs
4. Need for efficiency, modularity and scalability of mobile machinery
1) Software complexity
On one hand, new, more efficient and safer machine functionalities are strongly dependent on their software. A source of increased software complexity is the number of written lines of code, which easily can exceed 100,000 lines for only one state-of-the-art aerial platform controller.
On the other hand, safety standards for mobile machinery are constantly evolving – highly influenced by automotive regulations. Manufacturers of off-highway vehicles that are also in use on roads, should pay attention to integrate common technologies, comply with certain regulations and follow relevant trends of the automotive industry. For example, the first edition of ISO 26262, the international standard for functional safety of road vehicles, was revised in 2018 (ISO 26262:2018) to include heavier road vehicles (weight >3.5t) such as buses and trucks. Suppliers of electrical and/or electronic (E/E) systems are now confronted with higher requirements for the entire hardware and software development.
These are just two examples of the burden on new software development processes.
2) Innovation pressure
Higher software complexity goes hand-in-hand with the evolution of tools needed for development support. Disrupting technologies like IoT and cloud solutions or assisted, semi-autonomous or autonomous functionalities for mobile machinery are mainly software-driven and require talents and competencies at the right places. On top of that, due to the proceeding evolvement of consumer electronics and the related improved user experience (UX) and operating comfort expectations of mobile machinery operators are rising too. Even if modern consumer devices cannot withstand the harsh operation environment of off-highway vehicles, customers expect the same UX and interoperability as their electronic commodities. These trends have a profound impact on the required skills of the engineers, and on the product offering. For example, software development has transitioned from straightforward and linear PLC programming handled by one engineer to object-oriented design (OOD), Qt or even web technologies development done in diverse and geographically dispersed teams. On the product side, the HMI Team at TTControl has developed and recently launched its new rugged operator interface Vision 3 which supports OOD, relational databases, Qt and much more.
3) Resources, tools and costs
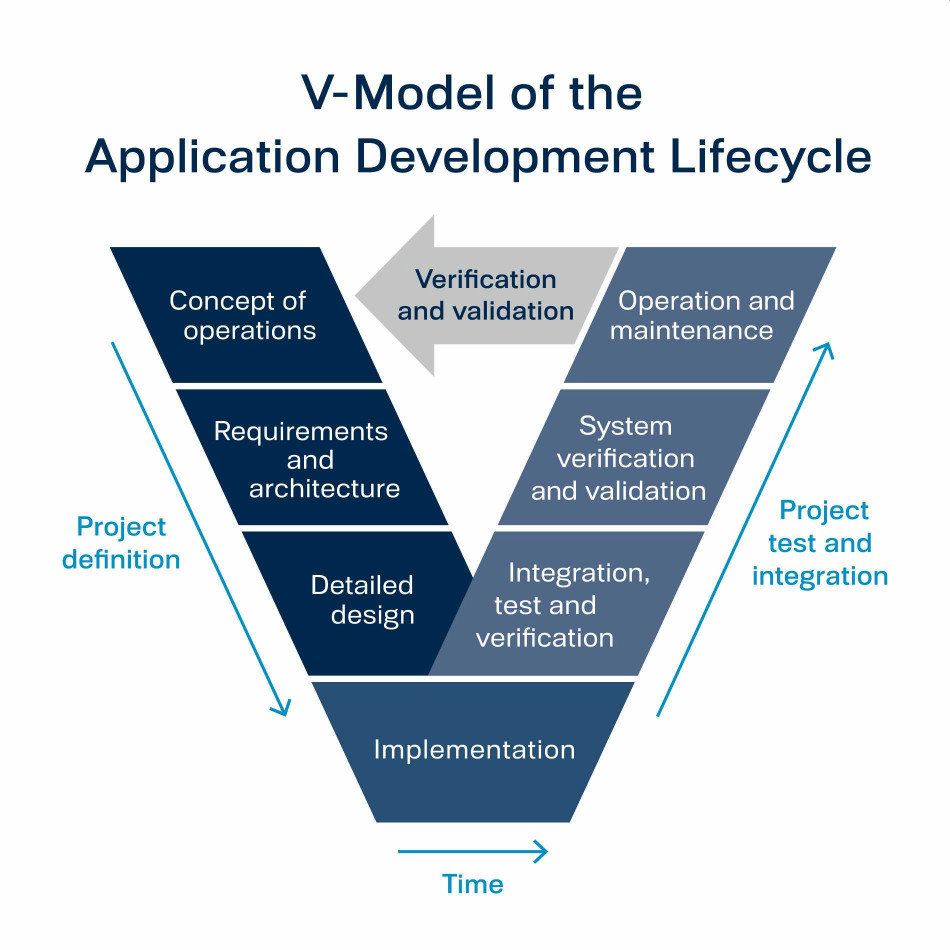
Software development needs complex infrastructure for e.g. versioning, bug tracking, compiling, debugging or testing. For an OEM of mobile machinery, this can be very challenging as its core competencies might not lie in software engineering itself. OEMs could be confronted with recruiting or training for adequate software developers. Besides qualified personnel resources, processes and tools also become essential to support software technicians along the entire development cycle (from the requirements capture to the automated software tests) The initial investment, the continuous maintenance and the alignment within the internal processes should be thoughtfully planned and covered by an adequate environment framework. Electronic suppliers inhering dedicated application development centers can support OEMs accelerating vehicle development and increase efficiency, resulting in a beneficiary contribution to entrepreneurial success.
4) Efficiency, modularity and scalability
Software modularity and scalability is highly essential for improving mobile machinery and its ROI over the entire product life cycle. OEMs will be able to make the most out of their products by focusing on modular solutions and economies of scale alone. The re-use of well tested and therefore reliable software library blocks allows also a significant reduction of risks. In order to comply with functional safety and international quality standards, cross-functional teamwork and well-established processes are needed to contribute to the OEMs efficiency properly.
TTControl offers very practical support for OEMs as Roberto Ferrari, Member of the Board of TTControl, says: “TTControl is aware of the numerous challenges OEMs are facing in the competitive mobile machinery market and has established a competence center for future application software development, accompanying its customers with their projects and help to shift mobile machinery to a new technological level.”
OEMs benefit from dedicated Application Development Center
With the dedicated Application Development Center (ADC) in North Italian Bressanone (Brixen), TTControl supports its customer along the entire machine development life cycle: from the definition of the requirements to the validation of the application on the machine.
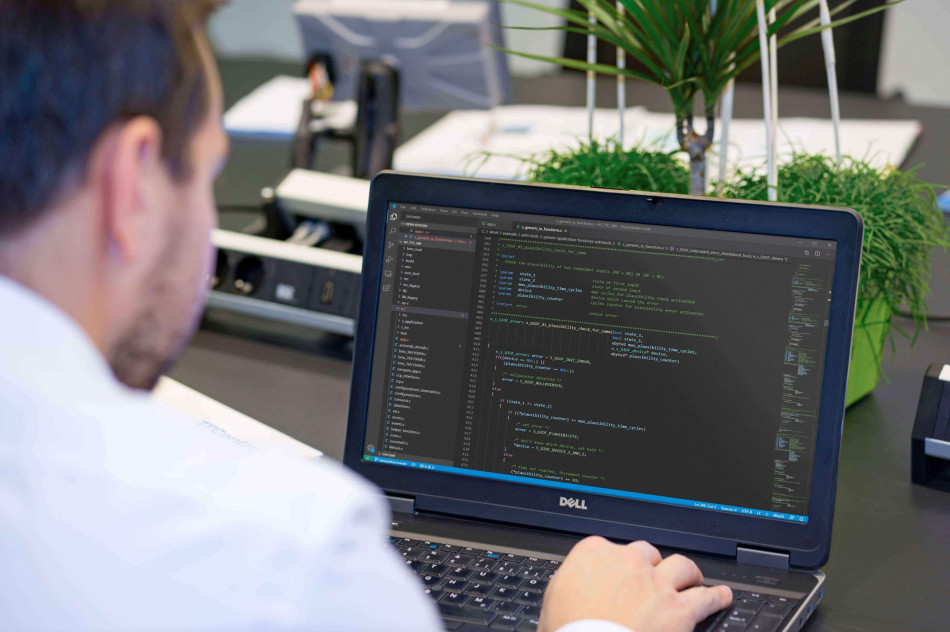
A team of engineers is at place, well-trained on functional safety, machine automation, HMI applications, IoT and computer vision. With more than 15 years in several application fields including agriculture, construction, municipal and material handling, the software engineering experts at TTControl fully comprehend their customers’ requirements and needs for mobile machinery design.
Janosch Fauster, Manager of customer projects at TTControl, describes the benefit for OEMs: “With the ADC we strive to be a reliable and flexible long-term partner for our customer’s software developments. We want to support the OEMs in continuously evolving their machine’s features, work efficiency and degree of automation with safe, state-of-the-art and maintainable software functions.”
Besides standard environments like C, C++, CODESYS, Qt or Simulink, TTControl has access also to the software solution MATCH, for customers relying on an integrated software approach for mobile machinery. MATCH is developed by HYDAC's Software Center in Großbeeren near Berlin. With this product line, HYDAC offers its customers a comprehensive software suite for the development and maintenance of electronic control systems for off-highway vehicles.
One-Stop solution made in Europe
Due to its integration into the TTTech Group and the Joint-Venture partnership with the systems, sensors and hydraulics company HYDAC International, TTControl can draw from extensive industry knowledge. During project phases, software engineers of TTControl can also rely on experts at TTTech Auto Iberia (Linux, Qt, computer vision, security, former Silicon Gears), TTTech Auto CEE in Bosnia and Herzegovina (embedded software and testing, former RT-RK) and the specially founded Covision Lab in Bressanone (computer vision research).
Focusing on their core business while relying on professional innovation partners helps OEMs to bundle their resources and to lead technological development.