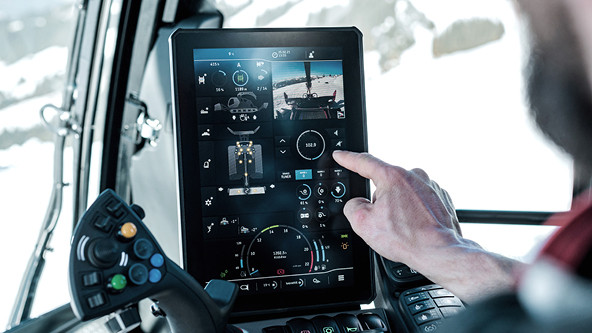
PRINOTH announced the new generation of its best-selling snow groomers, the LEITWOLF and the BISON. The electronics in high-tech snow vehicles must not only withstand extreme temperature fluctuations, ice and frost, but also meet highest requirements in terms of usability. An international team was assembled to design a state-of-the-art cabin that combines the highest standards of user-friendliness and design. Thanks to Continuous Delivery, TTControl ensured a shorter time to market and made the UX Design Award-nominated cockpit possible.
The initial vision was to make the machine’s complex work processes easy to control. The new PRINOTH Control Unit was to consist of an ergonomic multifunction joystick, a keyboard and a touchscreen display – all intuitive to operate, even when wearing winter gloves and snowsuit.
It was clear that all parties involved must coordinate very closely during the development process. The high complexity of the system architecture and the high proportion of different companies from different countries posed a number of hurdles. In addition to specialists for machines, various disciplines such as software and hardware developers, graphic designers and experts for user interface and user experience (UI/UX) worked together in close cooperation.
Continuous Delivery and changing requirements
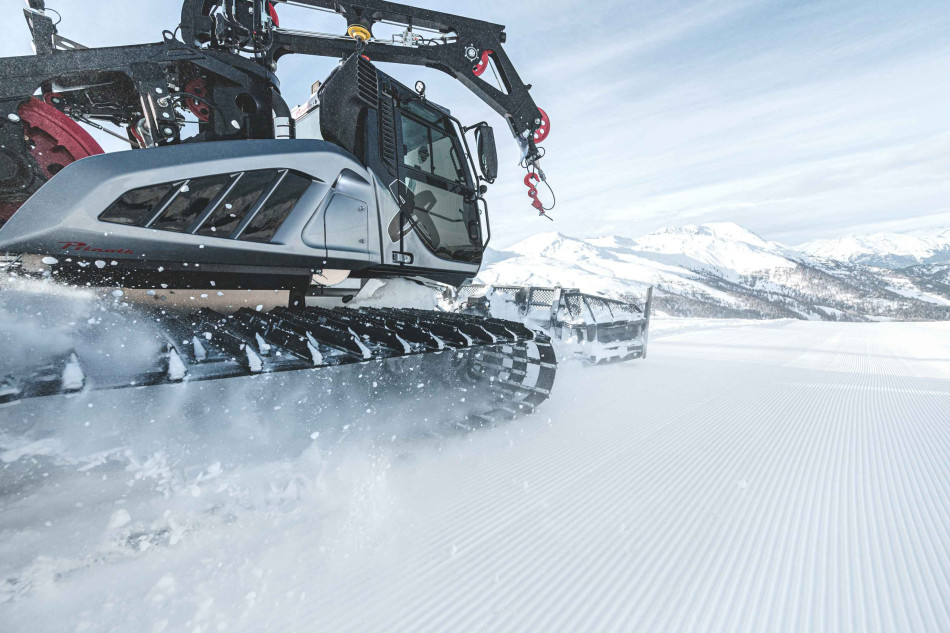
It wasn’t by chance that TTControl was involved with its latest 12-inch Vision 3 touchscreen display. Vision 3 enables operation at extreme temperatures of -30° to +70° C without loss of performance. The display works without restrictions in cold weather, but also when heat develops due to high levels of sunlight on the glacier. The die-cast aluminum rear housing design ensures passive cooling.
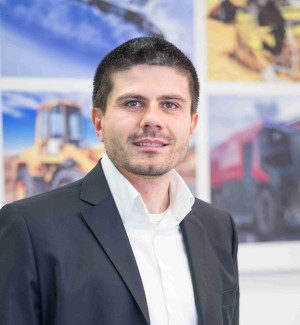
“One of the biggest challenges was the continuously evolving requirements,” says Janosch Fauster, Director of the Application Development Center at TTControl. “During the course of the project, our agile development process allowed us to keep adding new functions and workflows of future display users and provide them to the customer for testing. The prompt customer feedback helped us to quickly optimize the user interface and the implemented functionalities.”
Software versions with new features were created in very short, one-week sprints thanks to the flexibility of the individual team members as well as the robust and reliable development, project management, deployment processes and tool chain.
“This agile project management with its Continuous Delivery approach, along with the close collaboration with our customer PRINOTH were an important key to success,” says Janosch Fauster. “This not only ensured development in close coordination with the changing requirements, but also a shorter time to market.”
Agile development with Continuous Delivery is a software engineering approach in which teams implement software functions in short cycles, known as “sprints,” and make them available to the customer immediately. This means that the customer is involved in the development from the beginning of the project and can test the product and provide feedback early on. This reduces costs, time and the risk of incorrect development. In this way, incremental adjustments can be made throughout the development phase.
Intuitive operation thanks to a modular software architecture
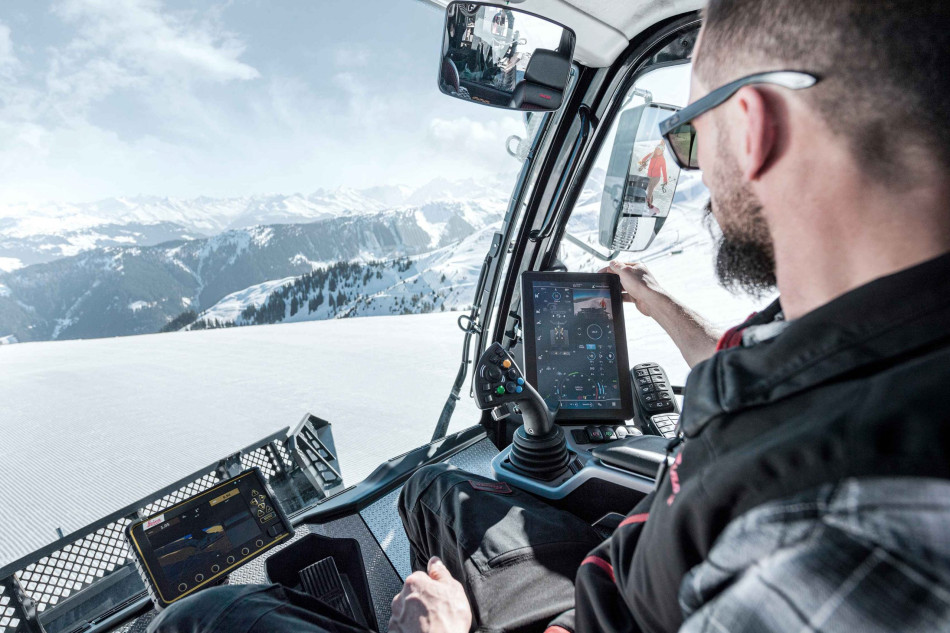
The cockpit, which has been nominated for the UX Design Award, was to contain a large number of components. These included numerous elements of a fully digital cockpit, such as a digital speedometer, a radio, a hands-free system and air conditioning controls. In addition to several cameras, it also includes map material, diagnostic tools and internet access, as well as a connection to SNOW HOW, PRINOTH’s digital services. Here, fleet operators in ski resorts have access to the current snow measurement of each vehicle, detailed statistical evaluations of vehicle data and productivity, as well as access to real-time data for diagnostics.
A system architecture for these many different components is highly complex. This was ideally solved by a robust and modular architecture on the software side. For this purpose, a large number of modules were developed, each of which performs specific tasks independently and functions similarly to “widgets” in smartphones. This modularity facilitated testing and enabled periodic feature releases.
On the operator side, this modular technological structure was developed together with experienced UI experts into a responsive, freely configurable and easy-to-use user interface.
The result: TTControl’s 12-inch touchscreen display provides quick access to all important functions on PRINOTH’s snow groomers. The driver can switch between the options with the push of a button – and thus adjust the light or use the reversing camera, for example, without losing sight of the settings of the tiller.
Parts of the screen content can also be customized and quick accesses can be created. Intelligent connectivity in the ski resort, central user management and integrated information on vehicle maintenance additionally facilitate intuitive slope preparation – in all weather conditions and at an incline of up to 100 percent.
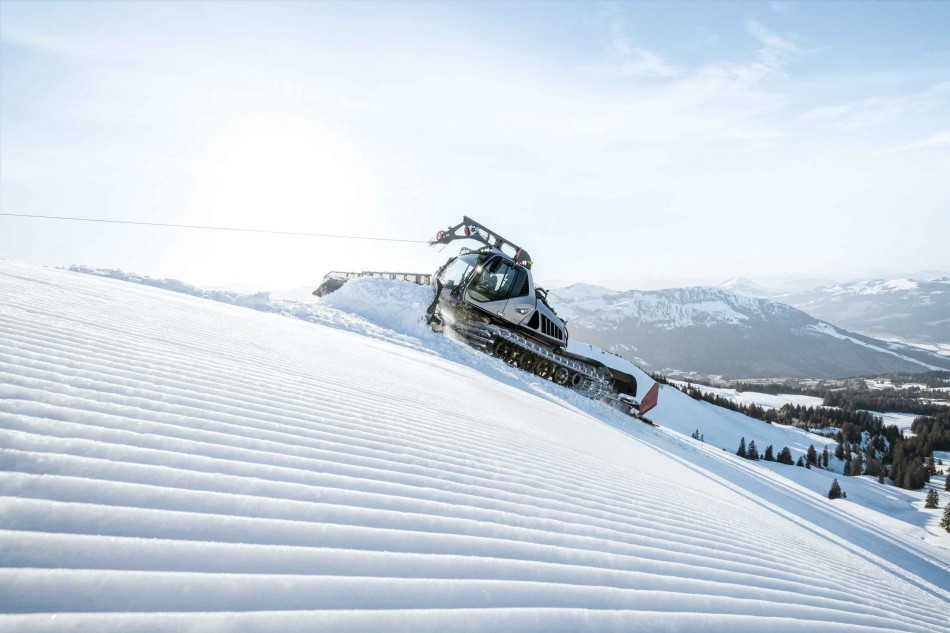
The findings
The prevalence of smartphones and tablets poses major challenges for manufacturers of mobile machines worldwide. A similar contemporary design, intuitive usability and lag-free display have become a standard expected in the mobile workplace and offers many advantages for operators and fleet operators.
“How user-friendly and contemporary a display becomes and whether this is already taken into account in the development process depends heavily on the UI/UX,” says Janosch Fauster. His advice: “Get the UI experts on board as soon as possible.”
The expert recommends combining a “robust and modular software architecture with an agile Continuous Delivery approach,” which enables the timely addition and integration of new modules to be software-ready for the future, respond flexibly to the results of customer surveys and reduce development costs.
Photo credits: ©Wisthaler/Prinoth