The TTC 30XH, a member of the TTC 30 family, is a CANopen based, user-friendly and smart input/output module that can be utilized as flexible control system extension in mobile applications. TTC 30XH is used in combination with, and controlled by a controller electronic control unit, communicating with the device module via the standardized CANopen® protocol.
By mounting the controller control unit centrally on the machine and the I/O modules close to the sensors or actuators, a distributed electronic architecture can be implemented in order to reduce mounting time and cost for cabling.
In addition to the general purpose module TTC 30XH we are also offering a safety certified version. For detailed information please visit the specific product page of the TTC 30XSH variant.
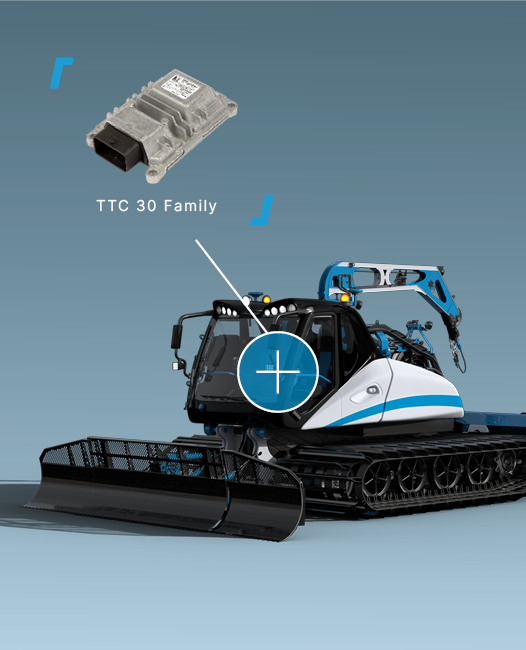
Stay Flexible with a Wide Range of Configurable I/Os
Both I/O module variants are designed for control of proportional valves and digital/analog outputs or inputs. They provide a wide range of configurable I/Os and allow local current control for its PWM outputs. The available safety variant is certified by TÜV Nord to comply with EN ISO 13849. The numerous configuration options enable the control system designer to compose a multitude of individual I/O sets.
Some machine manufacturers offer optional equipment for special work tasks (e.g. a winch, a crane or a lifting platform). The TTC 30XH I/O module is an easy-to-apply and economic solution for optional add-on equipment. It enables the separation of add-on equipment control from the standard machine control system helping to minimize the cost of the latter.
All TTControl I/O modules are protected by a compact aluminum die-cast housing which is highly suitable for the roughest operating conditions on mobile machinery. They come with a ready-to-run software and an electronic datasheet (EDS file). When the master is programmed in CODESYS®, the EDS file can be easily imported into the CODESYS development environment. This makes the setup user-friendly and saves development time.
Key Benefits
- Extensive I/O set with small form factor
- 30 I/Os with multiple configuration options per pin
- 5 variants offer flexible building blocks
- EN ISO 13849 PL c certified
- CANopen Safety
- Automotive-style aluminium housing for rough operating conditions
- High maximum current
- Easy integration and usage
- CANopen compliant
- Auto baud rate detection
- CAN termination configurable via connector pins
- Node-ID configuration via dedicated input pins